Alright, folks, gather around! Did you know that a makeup artist without their brushes is like a painter without their paintbrushes? Absolutely lost. That’s because makeup brushes are the unsung heroes of our cosmetic bags, magically transforming our faces from “I just woke up” to “I woke up like this.” They blend, contour, and highlight to create subtly natural and dramatically artistic looks.
Now, onto the juicy part that you’re all wondering about: how are makeup brushes made? It’s not just about sticking some bristles on a handle and calling it a day. Oh no, it’s a meticulous process involving choosing the right materials (we’re talking high-quality bristles that are softer than your pet cat), precise engineering (yes, there’s a bit of science behind those fluffy tools), and careful craftsmanship (an art form on its own). Imagine a symphony of materials together harmoniously to create the perfect tool for your 5-minute makeup challenge.
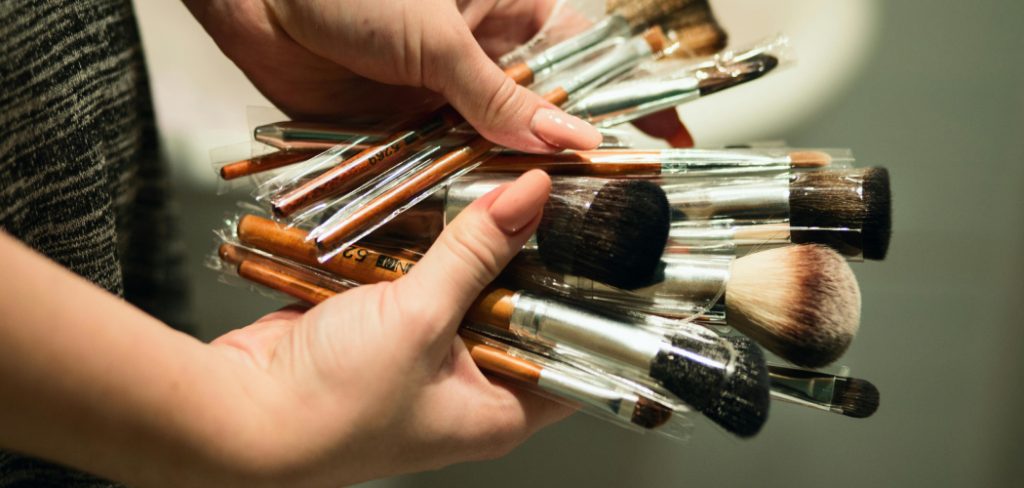
This guide aims to demystify the brush-making process, taking you on a behind-the-scenes tour from the initial sketch to the final product that lands in your makeup bag. Whether you’re a makeup aficionado, an aspiring beauty mogul, or just someone curious about how your tools are made, we’re here to spill all the tea (in a non-gossipy, educational way). Stick with us, and you’ll be a makeup brush connoisseur in no time.
Selection of Materials
Alright, folks, buckle up because we’re about to dive into the glamorous world of…materials! Yes, you heard it right. Before a makeup brush can grace your vanity table, we must pick its building blocks. It’s like choosing the ingredients for a gourmet meal, except nobody’s eating them.
A. Choosing Brush Handle Materials (e.g., Wood, Plastic)
First off, the handle. That part you grip tighter than your morning coffee. Handles can be made from various materials, each with its own flair. Wood gives you that classic, eco-chic vibe, making you feel like a nature goddess. Then there’s plastic, which, thanks to modern miracles, can look as sleek and luxurious as your favorite designer sunglasses. And do not forget the metal handles that scream “I mean business” when it comes to makeup applications. Choosing the right material is crucial; after all, it sets the stage for the makeup magic to happen.
B. Selection of Bristle Materials (e.g., Natural Hair, Synthetic Fibers)
Moving to the star of the show: the bristles. This is where things get fluffy. Bristles can be as diverse as the animal kingdom or as innovative as the latest tech in synthetic fibers. Natural hair bristles, sourced from goats or sables, are like the VIPs of the brush world, known for their softness and blending prowess. On the flip side, synthetic fibers are the rising stars, beloved for their vegan credentials and knack for precision. Plus, they’re champions at handling liquid and cream products without getting clumpy. It’s like having a tiny superhero at the end of your brush.
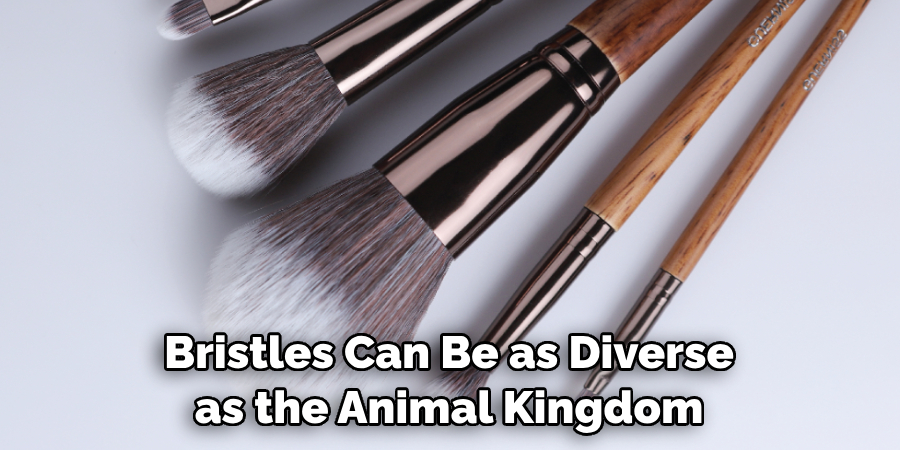
C. Importance of Quality and Durability
Now, why fuss over materials like it’s the match of the century? Because quality and durability are the names of the game. A brush that sheds more than your pet or snaps like a twig mid-application is a hard pass. You want tools that not only create art on your face but also stand the test of time (and countless washes). Investing in quality means brushes that stay loyal, performing at their peak, blending like a dream, and not bailing on you when things get tough (or when you’re running late).
Remember, in the kingdom of makeup, your brush is your scepter. Choose wisely, treat them well, and your reign shall be long and beautiful.
Handle Production
Alright, strap in because we’re about to get into the nitty-gritty of handling production. It’s like the “how it’s made” segment you never knew you needed for your makeup brush handle. Trust me, it’s cooler than it sounds.
A. Mold Design and Creation
First up, we’ve got mold design and creation, a process that’s more intricate than plotting your weekend brunch. Designers whip out their tools to sculpt the blueprint of your future handle. It’s like architecture but tinier and, arguably, more fun. They consider ergonomics – because no one likes a cramp mid-smokey eye – and aesthetic appeal, ensuring your brush handle won’t look out of place next to your chicest makeup products.
B. Injection Molding Process for Plastic Handles
Next, we venture into the world of injection molding for plastic handles – it’s like baking, but instead of cupcakes, we’re making brush handles. Molten plastic is injected into the meticulously designed molds (remember those from a second ago?), then cooled to harden into the desired shape. This process is almost as satisfying to watch as those videos of cake icing.
C. Turning and Shaping Techniques for Wooden Handles
Last but certainly not least, we have the turning and shaping techniques for wooden handles – imagine a pottery class but with wood. Craftspeople take rods of wood, and as they spin, they’re carved into the familiar shapes we love. It’s a dance between man and machine to create something that feels just right in your hand. This step is all about bringing that eco-chic, nature goddess vibe to life, with a touch of old-world craftsmanship that makes each brush slightly unique.
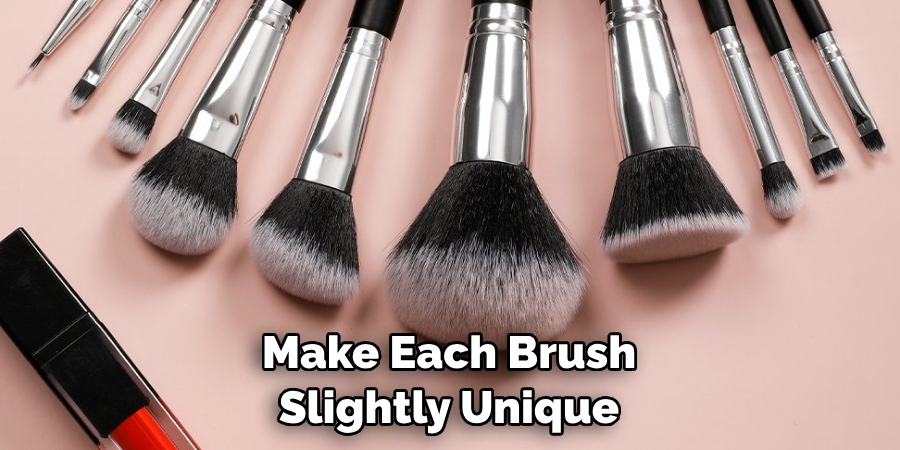
And voila! That’s the down-low on how makeup brush handles come to be. From sleek plastics molded into perfection to wooden pieces carved with finesse, it’s a process filled with precision, artistry, and a dash of magic. Next time you pick up a makeup brush, give a little nod to the journey its handle went through – from a mere concept to your trusty tool.
Bristle Preparation
Okay, it’s time to zoom in on the business end of the brush – the bristles! This part is like casting the lead roles for your very own blockbuster (except your movie is about making stunning makeup looks come to life).
A. Sourcing Natural Hair from Ethical Suppliers
First off, if our brush is going Hollywood, then natural hair bristles are the A-listers with a conscience. We’re talking about sourcing goat, sable, or pony hair, but only from suppliers who treat their stars with the respect and kindness they deserve. Imagine a green room, but for goats – that’s the level of VIP treatment we aim for. It’s all about keeping things ethical and ensuring our furry friends are living their best lives while contributing to your flawless foundation.
B. Synthetic Fiber Production and Blending
Now, onto the tech-savvy new kids on the block – synthetic fibers. This process is like the CGI of the makeup brush world: cutting-edge, innovative, and capable of creating some mind-blowing effects. These fibers are made from materials like nylon or polyester and are blended in a way that would make a smoothie jealous. The goal? To achieve the perfect balance of softness, durability, and an uncanny ability to work with any makeup formula. It’s the future, folks, and it’s looking fabulous.
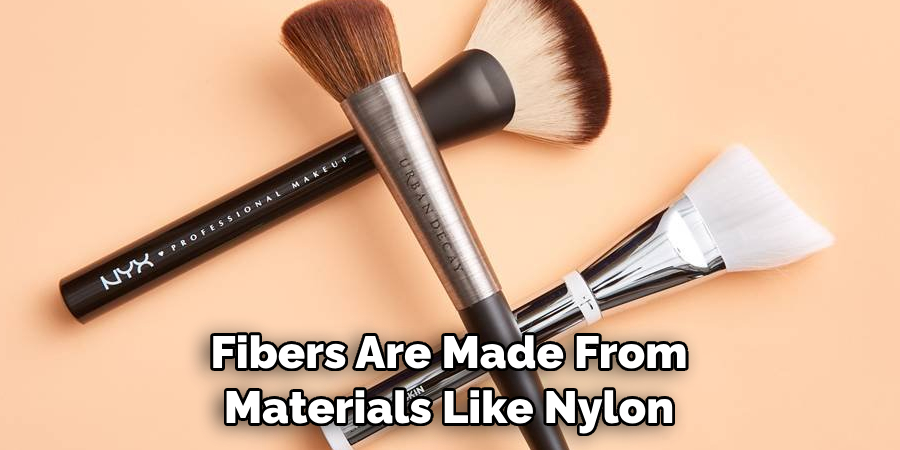
C. Sorting and Trimming Bristles to Uniform Lengths
Last in our behind-the-scenes tour, but certainly not least, is the sorting and trimming of those glorious bristles to uniform lengths. Think of it like a styling session for the Met Gala; every bristle needs to be on point. Precision is key, as a brush’s effectiveness is directly tied to its shape and the consistency of its bristles. This step is a blend of technology and artistry, with machines and skilled workers teaming up to ensure every bristle is just right. The result? A makeup brush that’s as ready for its close-up as you are.
And there you have it, the scoop on how those bristles come to be. From ethical star treatment to futuristic fibers and a finishing touch that’s all about precision, it’s a process that’s as fascinating as it is meticulous. Next time you sweep that brush across your cheek, remember the journey those bristles went through to help you shine.
How Are Makeup Brushes Made: Ferrule Formation
Alright, makeup mavens and brush buffs, buckle up as we deep-dive into the unsung hero of our makeup brush ensemble – the ferrule! This shiny, cylindrical champ might not get all the glamour shots, but believe me, it’s pivotal to holding the whole star cast together.
A. Metal Ferrule Production (e.g., Aluminum, Brass)
First off, the saga of ferrule production kicks off with selecting the metal with more care than choosing your Friday night outfit. Aluminum and brass are the top choices, kind of the VIP metals of the ferrule world. Why? They’re durable, resistant to corrosion (because no one wants a rusty brush), and have that shiny allure that makes every makeup application feel a bit more special. The metal sheets are cut and rolled into their iconic cylindrical shape—imagine rolling sushi, but less delicious and more metallic.
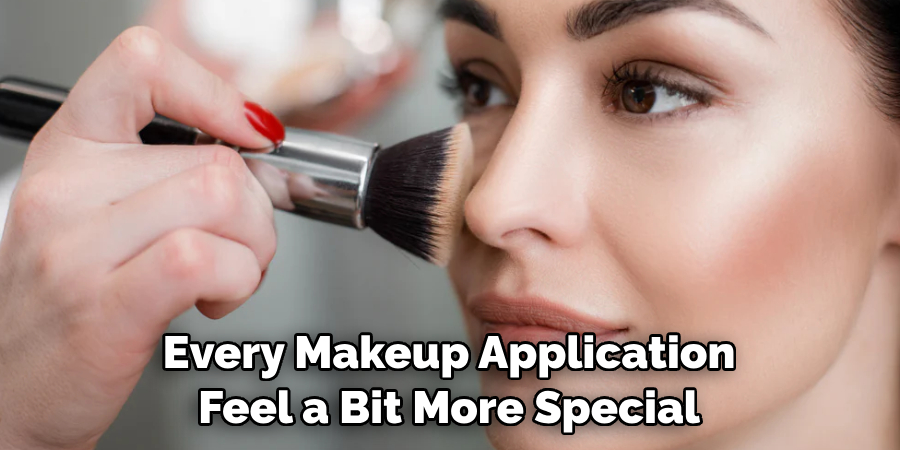
B. Shaping and Soldering Techniques
Next up, shaping and soldering these babies is an art form that would make even the most seasoned blacksmith nod in approval. The metal tubes are finely shaped to ensure they snugly fit the brush handle on one end and the bristles on the other, creating a smoother transition than a fresh jar of peanut butter. Soldering comes in to lock everything in place; it’s like the security bouncer at the club, making sure no bristles party too hard and escape.
C. Quality Control Measures for Ferrules
Finally, because we’re all about that high-quality, no-drama makeup application, quality control for ferrules is stricter than your grandmother judging your outfit. Each ferrule undergoes a rigorous inspection, ensuring it’s not too tight (no one likes a brush that sheds faster than a cat in summer) and not too loose (because floppy bristles are a big no-no). This step is all about guaranteeing the ferrule’s durability and fit, making sure it will hold up against the rigors of daily use, from that light, breezy swipe of blush to the intense, focused dab of concealer.
And there you have it, the lowdown on the ferrule formation—where science meets sorcery to create the unsung hero of your makeup bag. Next time you blend and buff to perfection, give a little mental high five to the ferrule for keeping it all together.
How Are Makeup Brushes Made: Assembly Process
Alright, team, strap in because we’re hitting the home stretch of our makeup brush saga – it’s assembly time! This is where all our brush parts come together in a high-stakes, glitzy reality show finale where everyone’s a winner.
A. Inserting Bristles into Ferrules
Picture this: The bristles, all jazzed up and nowhere to go, finally meet their match with the ferrule. It’s like setting up the perfect blind date between two seriously compatible singles. The bristles are gently but firmly inserted into the ferrule, ensuring no strand is left behind. It’s a delicate balance, kind of like trying to get the last bit of toothpaste out of the tube without making a mess.
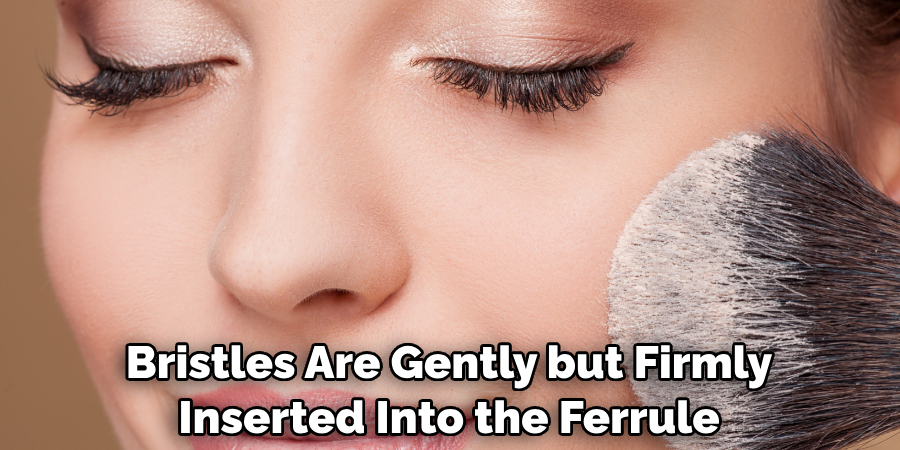
B. Securing Ferrules to Brush Handles
Next up, we’ve got a real Cinderella moment as each ferrule finds its perfect fit with a handle. This step is crucial; we’re talking about a lifelong bond here, folks. The ferrule is secured onto the brush handle with the kind of precision that would make a Swiss watchmaker weep. It’s the moment when everything comes together, and suddenly, it’s starting to look a lot like the makeup brush we’ve been dreaming of.
C. Adhering Bristles with Epoxy Resin
The grand finale, the pièce de résistance, comes when we break out the epoxy resin—makeup brush glue that could hold together the friendships in a reality TV show. This resin is applied to secure the bristles within the ferrule, ensuring that they’re set to stay, come what may. It’s like that final spritz of hairspray before you step out, confident that not a hair will be out of place. The bristles are then left to cure, dreaming of the day they’ll finally grace your cheek with their presence.
And that, my friends, is the assembly process in all its glory. From a bunch of disparate parts to a cohesive, ready-for-action makeup brush that’s destined to be your new BFF. Every time you wield that brush, remember the epic journey it’s been on. From the ethical sourcing of its bristles to the meticulous craftsmanship of its handle and ferrule, every step is a testament to the art and science of making something truly magical.
Trimming and Shaping
Alright, get ready to snip, snap, and shape because we’re moving on to the world of trimming and shaping our beloved brush bristles. Think of it as taking your brush to the hairdresser for a chic new do.
A. Cutting Excess Bristle Lengths
First off, we’ve got the cutting of excess bristle lengths – it’s like giving the brush a good, old-fashioned haircut. This step ensures that all the bristles are even stevens, making for a smooth, even application when you’re painting your masterpiece (aka your face). Imagine trying to paint the Mona Lisa with a raggedy old brush – not happening, right? That’s why this step is crucial.
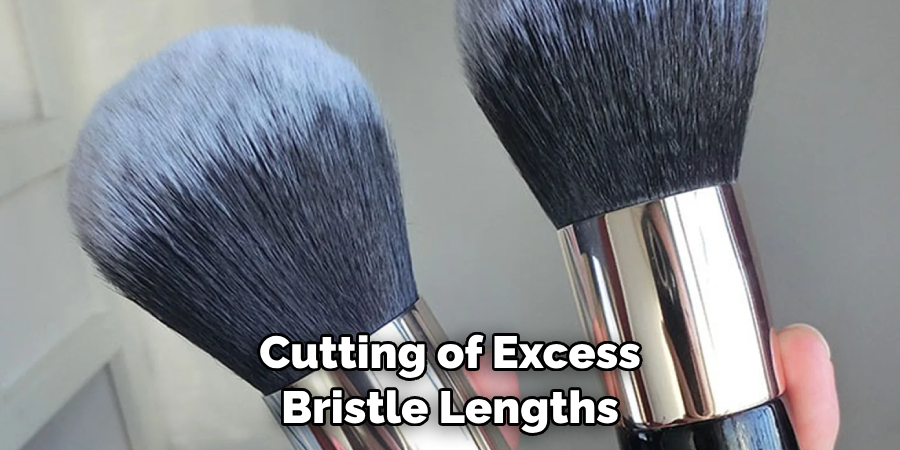
B. Shaping Brushes to Desired Styles (e.g., Angled, Round)
Next, it’s time to get fancy with the shaping. Whether you’re a fan of the classic round, the chic angled, or the bold flat-top style, this is where each brush starts to show its true colors (literally). Shaping the brushes to desired styles is like choosing the outfit for the day; it sets the tone for everything that follows. Want to contour like a Kardashian? You’ll need that angled brush. Looking for that airbrushed finish? Say hello to your new best friend, the round brush.
C. Quality Inspection for Uniformity
Last but not least, we can’t send our brushes off into the world without a final check under the microscope. This quality inspection for uniformity is like the final rose ceremony in “The Bachelor” – only the best brushes make the cut. Each one is scrutinized to ensure it’s not just ready for the big leagues but also won’t ghost you after a few uses. We’re talking no stray bristles, perfect symmetry, and the kind of uniformity that would make a drill sergeant proud. It’s a tough world out there, but these brushes are built to last.
And there you have it, folks, the grand trimming and shaping extravaganza. From a bunch of unruly bristles to a lineup of perfectly coiffed beauty tools ready for their debut on your vanity. Remember, every time you dab, blend, or sweep, there’s a whole lot of love, precision, and a bit of hair salon magic that went into making your makeup brush.
Cleaning and Sterilization
Guess what time it is? That’s right, it’s time to give our newly minted brushes a bath—not the kind with bubbles and rubber duckies, but close enough. Cleaning and sterilization are like the spa day for brushes, ensuring they’re squeaky clean and ready to face the world (or your face, to be exact).
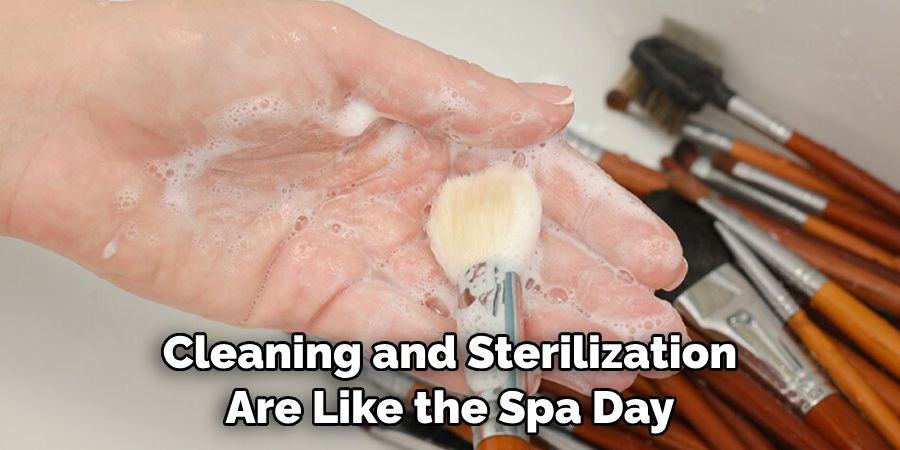
A. Removing Residual Manufacturing Residues
First, we’re dealing with the nitty-gritty of removing those pesky residual manufacturing residues. These brushes undergo a thorough scrubbing session, removing any leftover glues, dyes, or existential dread from the assembly process. Think of it as exfoliating after a long day; it’s refreshing and leaves the brushes feeling brand new.
B. Sterilizing Brushes for Hygienic Use
Next, it’s time to zap any germs with our good friend, Mr. Sterilization. This process is like sending the brushes through a boot camp for germ warfare, ensuring they’re 100% ready for action and won’t cause a breakout faster than a high school romance. Using high-tech methods like UV radiation or autoclaving, every brush is made safe for even the most sensitive of skins.
C. Packaging Brushes for Distribution
Finally, it’s the moment we’ve all been waiting for—dressing up our brushes for the big debut. Packaging these beauts is like tucking them into their prom dresses, all shiny and new, ready to be shipped off to stores and, ultimately, to make their mark in makeup bags around the globe. Each brush is carefully placed in its packaging, kissed goodnight (metaphorically speaking), and sent off with dreams of beauty transformations.
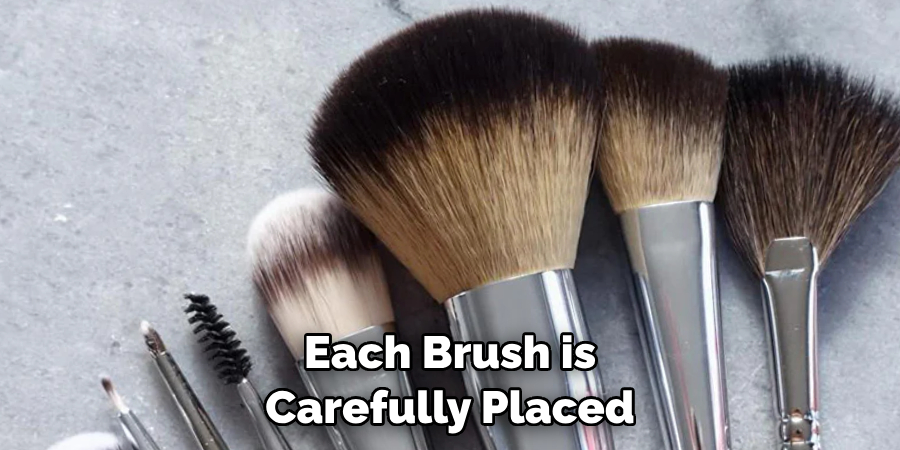
And voila! From a twinkle in a designer’s eye to a fully-fledged, clean, and sterilized makeup brush ready to take on the world—one face at a time. Remember, every time you sweep that brush across your cheek, there’s a whole saga of crafting, caring, and a spa day that went into making it just perfect for you.
Quality Control Measures
Welcome to the behind-the-scenes world where we make sure our makeup brushes aren’t just pretty faces—they’ve got the skills to back them up. In this chapter, we’re looking into the rigorous quality control measures that keep the makeup brush rebellion in check.
A. Inspecting Finished Brushes for Defects
First up on the quality control agenda is playing detective with our finished brushes. Each brush undergoes a top-to-bottom, CSI-level inspection to catch any renegades trying to sneak past our pearly gates. We’re talking microscopic scrutiny here, folks. If a brush has so much as a hair out of place, a wonky handle, or looks at us funny, it’s getting the boot. This step ensures that only the most perfect, selfie-worthy tools grace your beautiful face.
B. Testing Bristle Firmness and Flexibility
Next, we get into the gym phase for our brushes—testing the bristles’ firmness and flexibility. It’s like putting our brushes on a workout regimen, where they must prove they’re tough enough to handle the smoky eye workout but flexible enough for a soft, natural look. We bend, we twist, and we press to make sure these brushes can take what you dish out. Only the strongest, most adaptable brushes earn their right to party in your makeup bag.
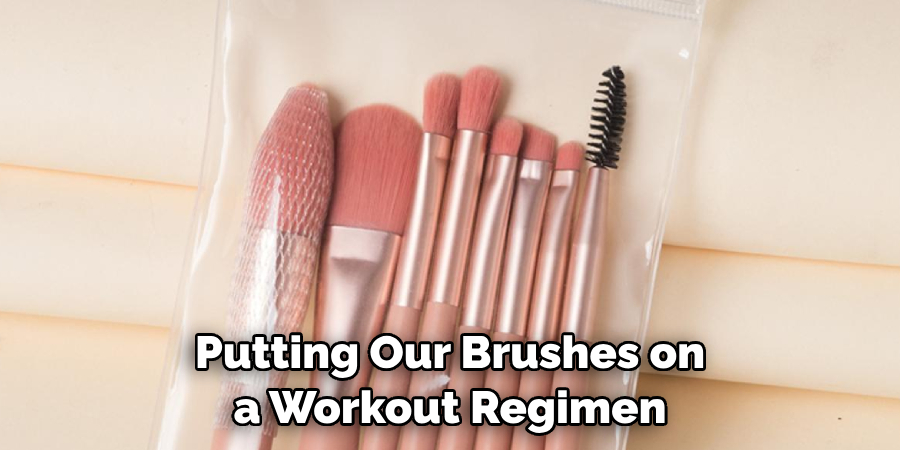
C. Ensuring Compliance with Safety Standards
Last but certainly not least, we put on our safety goggles and ensure every brush is up to snuff with the strictest safety standards. It’s like the final exam where the brushes need to pass with flying colors or it’s no graduation cap for them. We’re checking for chemicals and irritants and making sure they’re as hypoallergenic as your grandmother’s famous apple pie. Because the only surprise we want you to have is how amazing your makeup looks—not an unexpected skin reaction.
And there you have it, folks—the grand tour of the makeup brush boot camp known as Quality Control Measures. From the intense scrutiny for defects to the physical fitness test of bristles and safety standard compliance checks, it’s a tough world out there. But rest assured, by the time a brush makes its way to you, it’s been through the wringer and come out gleaming, ready to face whatever makeup challenge you throw its way.
Environmental Considerations
Alright, eco-warriors, buckle up because we’re going green! In this day and age, it’s not just about looking good; it’s about doing good, too. We’re taking you through the maze of how we’re turning green with envy, not eco-friendliness. Welcome to the part of the saga where we talk about trees, recycling bins, and all that glitters sustainably.
A. Sustainable Sourcing Practices
First on the list, we’ve got sustainable sourcing practices. Imagine choosing ingredients like you’re swiping on a dating app. Left for the no-gos and right for the “Oh, yes!” that meets our eco-criteria. We’re not just picking up any material; we’re looking for the ones that whisper sweet nothings about their low impact on the planet. We’re all about that sustainable romance, from handles that could have been starring in their forest saga to bristles that didn’t start their life with a carbon footprint the size of a yeti.
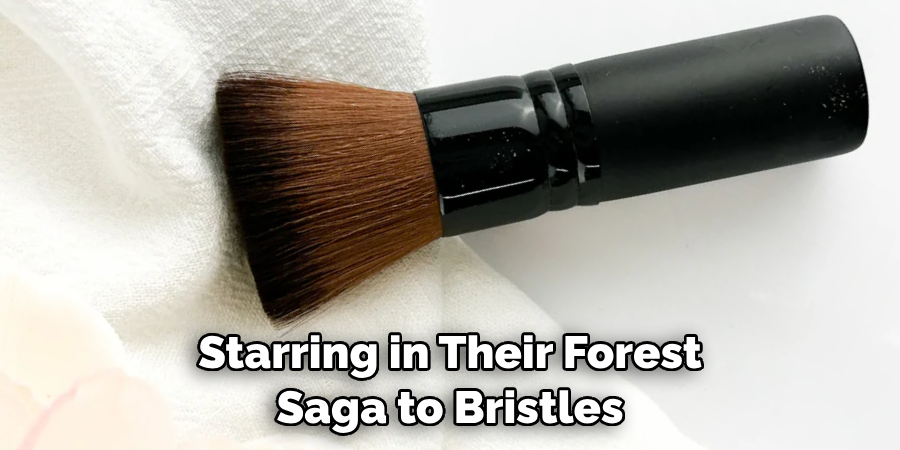
B. Recycling and Waste Management Efforts
Next up are recycling and waste management efforts—it’s like the cleanup crew after a wild party but for our manufacturing process. We’ve got bins lined up like soldiers, each one ready to take on different types of waste. Metals, plastics, and misfit bristles all find their way into their own eco-friendly after-parties. And it’s not just about tossing things into bins willy-nilly; we’re talking about a master plan that involves reducing, reusing, and recycling like it’s going out of fashion. We’re here to make sure our footprint is as light as a feather, even if it’s from a synthetic, hypoallergenic feather.
C. Innovations in Eco-Friendly Materials
And now, for the grand finale—innovations in eco-friendly materials. Picture this: scientists and designers sitting in a tree, K-I-S-S-I-N-G. First comes love, then comes marriage, and then comes a makeup brush made with materials that would make Mother Nature swoon. We’re not just sticking to the old classics; we’re searching for the next best thing in eco-friendly materials. Biodegradable, recyclable, and with a backstory so green it might as well photosynthesize. These innovations aren’t just for show; they’re here to redefine the makeup game by being as gentle on the planet as they are on your skin.
And there you have it, folks—the scoop on how we’re turning the makeup brush world upside down, one eco-friendly step at a time. From the ground up, we’re making strides in sustainable sourcing, waste management, and pioneering materials that could make even the most environmentally indifferent person start composting. Remember, every swipe of your eco-chic brush is a small victory for the planet.

Conclusion
To wrap this up, we’ve whisked you away on a magical mystery tour of “how are makeup brushes made,” unveiling every stage from the “Eureka!” moment in design to the final, fabulous flick of a perfectly crafted brush. It’s been an epic saga of selecting primo materials, shaping them with the finesse of a sculptor, and then undergoing the beauty equivalent of boot camp with our rigorous quality control.
We’ve chatted about the obsession with quality that makes each brush worthy of your makeup mastery, the craftsmanship that’s as precise as your eyeliner on a good day, and our green-hearted dedication to sustainability. Our brushes aren’t just tools; they’re treasures, crafted with care, destined to dance across your face with the light touch of a butterfly wing.
Finally, taking a moment to appreciate the artistry behind makeup brush production illuminates the dedication and innovation interwoven in every step. It’s a blend of tradition and cutting-edge technology, all sparked by the question of how makeup brushes are made. This leads to creations that not only enhance beauty but also tread lightly on our planet. Every stroke with our brushes reminds us of this beautiful intersection between form, function, and caring for Mother Earth.
About the Author
Jane Hubbard is a passionate beauty expert with a wealth of experience in makeup, hair, and overall beauty techniques. After years of working as a hairdresser specialist, she followed her entrepreneurial spirit and started her own consultancy business.
Jane has always been driven by her desire to help others feel confident in their own skin, and she does this by sharing her knowledge, experiences, and practical beauty tips. Through her consultancy, she empowers individuals to embrace their unique beauty, offering tailored guidance that boosts both self-esteem and personal style.
Professional Focus
- Specializes in makeup, hairstyling, and beauty consulting.
- Provides personalized beauty advice, tips, and techniques to help individuals feel confident in their appearance.
- Dedicated to staying up-to-date with the latest industry trends and developments.
- Passionate about creating a comfortable and empowering experience for every client.
Education History
- University of Craft and Design – Bachelor of Fine Arts (BFA) in Woodworking and Furniture Design
- Woodworking Apprenticeships – Extensive hands-on training with skilled craftsmen to refine carpentry and furniture making techniques
- Online Courses & Masterclasses – Continued education in advanced woodworking techniques, design principles, and specialized tools
Expertise:
- Makeup artistry, hairstyling, and beauty consulting.
- Personalized beauty techniques to enhance confidence and self-expression.
- Educating clients on how to maintain their beauty routines at home.